Nexans Ultracker Smart Inventory Management Solution
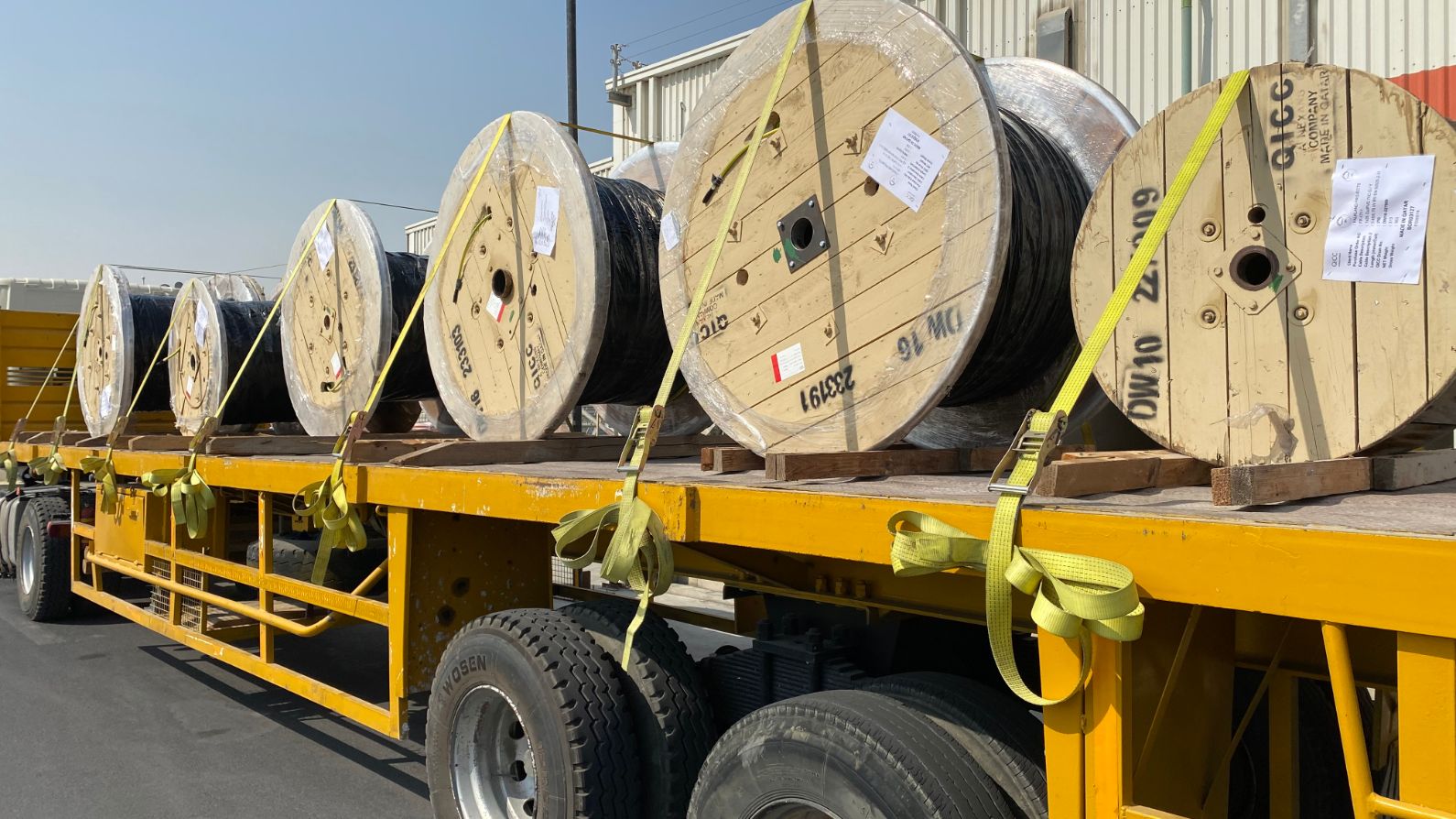
-
LOCATIONQatar
-
PARTNERSHIPFalkland
-
MARKETBuilding
Challenge: providing solutions to ensure a continuous production and avoid a lack of visibility of the multiple site inventories
The Smart Inventory Management Solution is combining RFID technology and modern supply chain methodologies. The solution is applicable for multi-suppliers and multi-products, composed of:
RFID labels tagged on drums, RFID signal receivers, such as handhelds and a dedicated Web platform
Solution: what is the operating mode?
- Step 1: all the Drums are tagged within QICC Nexans Factory with RFID labels. Simultaneously, stock appear on the web platform
- Step 2: the goods are shipped to our customer and are displayed with the status "In Transit" on the web platform
- Step 3: the goods arrive at customer premises and pass the RFID reception point of the warehouse. Drums are therefore registered as "Recevied" on the web platform and the quantities are automatically added to the customer stock level
- Step 4: the customer consumes a part of its stock and reach the pre-defined threshold level. At this point, the system is initiating an automatic and in real-time replenishment request towards QICC Nexans.
And then the process starts again.
Benefits: what's in it for the customer?
- First, the customer is able to get visibility of its stock in real-time. It will be possible to follow the products throughout the web platform. (24 hours/7 days)
- Second, is the registration of stock consumption in real-time, meaning that once pre-defined threshold levels are reached, replenishment alerts are sent in real-time. The replenishment is based on consumption and not anymore based on theoretical schedules.The inventory levels are aligned with customer’s demand and therefore avoid overstock.
- Third, is a quick reception process. The process of incoming goods reception is automated, tasks are simplified and accelerated . No need for paper handling, multiple data entries…
- Fourth, the physical stock counting will be fast and easy, due to the “inventory counting” functionality. As an example, all drums are in the Warehouse and emitting a signal which are received on the handheld at once, allowing to make a comparison between the current stocks and registered stocks in the platform. The deviations are immediately visible and contributing to time saving by avoiding to check drum by drum manually.
On the field, the experience gained with customers confirmed an inventory reduction of around 40%. As a consequence, to lower inventories, the need for storage surface is also going to be decreased. This decrease will have positive impacts on safety and handlings.
“ Even though the system has not yet been implemented completely, highly impressed and super excited with the trial period already implemented. It helps distributors and contractors notify the shortage of materials, inventory reports help for the best analysis and lead for best decision making.
”
Jees Thomas
Senior Business Development Executive, FalklandThe many benefits of Nexans Ultracker SIM solution, by Falkland:
Inventory notifications help to order the material in shortage
Helps to secure stock availability for end customers
Represents a systematic or accurate inventory solution
Reduces the logistics uncertainties
Supports the forecasts of budget, purchase and sales
Best solution for operations tracking
Reduces the unwanted material stock
Our websites
Select your country to find our products and solutions
-
Africa
- Africa
- Ghana
- Ivory Coast
- Morocco
- North West Africa
- Americas
- Asia
- Europe
- Oceania